Noticias
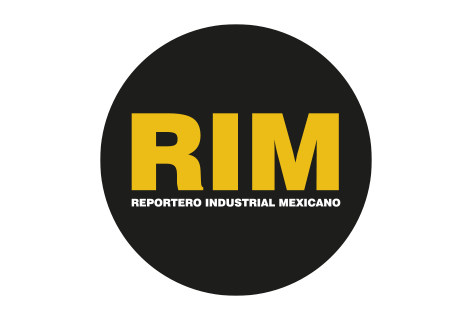
El panorama global de la manufactura de autos eléctricos es más competitivo que en décadas anteriores, ya que cada vez más fabricantes compiten para hacerse un hueco
Desde mediados de los años treinta, los «Big Three» (Tres Grandes) fabricantes dominaban el mercado automovilístico de Estados Unidos: General Motors, Ford y Daimler Chrysler. Y así continuó durante más de 70 años. Sin embargo, la competencia entre los fabricantes de autos está cambiando, tanto en Estados Unidos como en los principales mercados mundiales de manufactura de vehículos eléctricos (VE): Asia-Pacífico y Europa.
Según comenta Matthias Holweg en The Evolution of Competition in the Automotive Industry (Evolución de la competencia en la industria del automóvil), un capítulo del libro Build To Order: The Road to the 5-Day Car (Fabricar por encargo: el camino hacia el coche de 5 días): “La competencia ha pasado del liderazgo en costos durante el apogeo de la producción en serie original de Ford, a la variedad y la oferta [y después] a la diversificación mediante el liderazgo en diseño, tecnología o excelencia de fabricación.”
Esto también se aplica a los mercados de VE. Estos mercados se están presentando como más diversos y competitivos que los mercados automovilísticos de antaño, ya que grandes empresas consolidadas, como Porsche, compiten con pequeños fabricantes en expansión mundial, como Polestar.
Lea también: "¿A qué se enfrenta la cadena de proveeduría con las nuevas tendencias automotrices?"
Según Statista, a escala mundial, estas empresas tienen que ponerse a la altura de China; de hecho, seis de los diez vehículos eléctricos enchufables más vendidos en todo el mundo eran de marcas chinas en 2021.
Para los fabricantes de equipos originales (OEM), los mercados competitivos están cambiando las exigencias impuestas a las piezas. Los VE tienen menos piezas, más pequeñas y ligeras, y deben soportar mayores niveles de par del motor eléctrico, mayor eficiencia energética y aumentar la densidad de potencia. Esto, por supuesto, exige mucho de las piezas, lo que ha provocado un cambio en la tecnología de los materiales.
Los especialistas del fabricante de herramientas de corte para máquinas-herramienta, Sandvik Coromant prevén que este cambio incluya un aumento continuo del uso de aceros de alta resistencia, que pasarán de representar alrededor del 15% de todos los materiales utilizados en la fabricación de automóviles en 2010, al 38% en 2030. Estos nuevos materiales, incluidos los aceros limpios y ultralimpios, se fabrican con elementos de aleación y son capaces de resistir los retos mencionados –como los mayores niveles de par del motor eléctrico– porque tienen menos impurezas metalúrgicas.
Pero, ¿cómo se relaciona esto con la maquinabilidad? Con los aceros limpios y ultralimpios, observamos un aumento de la plasticidad del material, ya que la reducción de impurezas en los aceros se traduce en retos de mecanizado relacionados con la capacidad de rotura y la eliminación de virutas.
Estos materiales tienen un alto rendimiento elástico que, a su vez, requiere mayores fuerzas de corte durante el mecanizado y crea mayores niveles de desgaste de la herramienta. Aunque los aceros de alta resistencia, limpios o ultralimpios son más difíciles de mecanizar, la creciente integración de la digitalización y la fabricación asistida por ordenador (CAM) en las líneas de producción está elevando los estándares de calidad y eficiencia de la fabricación.
Estos son los retos a los que se enfrentan los fabricantes de automóviles, y los que no actualizan sus procesos de producción o recurren al tradicionalismo corren el riesgo de quedarse atrás. Pero, ¿cómo pueden los fabricantes dominar las tendencias? La respuesta reside en una mejora de las máquinas herramienta, pero también en un nuevo método de mecanizado diseñado para optimizar la calidad y mejorar la eficacia, los tiempos de ciclo y el ahorro de costos, incluso en el mecanizado de aceros duros.
Mejor control de la viruta
Es bien sabido que un control eficaz de las virutas contribuye a la productividad y fiabilidad de los procesos de mecanizado, así como a la calidad final de las superficies mecanizadas. Examinemos más de cerca el control de virutas y cómo afecta a la productividad en el mecanizado y al desgaste de la propia herramienta.
Si la plaquita mecaniza la pieza en un ángulo cercano a 90°, el grosor de la viruta será igual a la velocidad de avance (fn); así, a una fn de 1 milímetro por revolución (mm/rev), la viruta tendrá un espesor de 1 mm. Si reducimos el ángulo de entrada, cuanto menor sea, menor será el grosor de la viruta. Es posible aumentar la fn en consecuencia. Así, por ejemplo, al disminuir el ángulo de entrada de 90° a 25° y aumentar la fn de 0.25 a 0.6 mm/rev, el grosor de la viruta seguirá siendo el mismo. El resultado es un mecanizado más productivo con los mismos niveles de control de virutas.
Un ejemplo de las tecnologías desarrolladas para enfrentar este reto es la metodología PrimeTurning, que incluye el mecanizado con un ángulo de entrada pequeño para ofrecer una productividad muy alta y una larga vida útil de la herramienta.
Este método permite a los clientes realizar torneados en todas las direcciones y, de este modo, pueden lograr una mayor eficacia y productividad que con el torneado convencional. Gracias a esta metodología se ha conseguido un aumento de la productividad y una mayor vida útil de las herramientas para los clientes.
No obstante, el proceso necesita herramientas específicas para aprovechar estas ventajas. Una herramienta convencional no permitirá los mismos niveles de control de virutas, ni los ángulos de incidencia adecuados, por lo que en la práctica no funcionará. Para ello, la firma Sandvik Coromant desarrolló herramientas como CoroTurn, cuyo último desarrollo es la segunda generación de plaquitas CoroTurn tipo B, que incorpora plaquitas negativas de doble cara con cuatro filos de corte diseñados para un mecanizado más rentable, junto con un nuevo diseño robusto del asiento de la punta y geometrías actualizadas. Con estas características, la herramienta puede realizar cortes más profundos (mm), con mayores velocidades de mecanizado (mm/rev) y fn, además de un mejor control de la viruta durante el mecanizado de aceros de alta resistencia y otros aceros duros.
Esto beneficia a la productividad, pero ¿qué pasa con el desgaste de la herramienta? Esto nos lleva al diseño de la propio inserto. Con un inserto convencional, el mecanizado con un ángulo de entrada menor hace que la mayor parte del calor y la carga recaigan en la esquina del inserto, que también resulta ser la parte más débil, con la menor cantidad de metal duro para absorberlo. En su lugar, cada inserto de la nueva familia de herramientas del fabricante sueco tiene cuatro filos de corte en lugar de dos, con esquinas más fuertes. Con más filos, se puede conseguir más mecanizado con cada inserto, mientras que el calor y la carga se reparten por una parte mucho mayor del filo de corte.
Lea también: "Las tecnologías de sujeción en máquinas-herramienta presentan retos permanentes"
La segunda generación de insertos también ha sido diseñada para superar los problemas que normalmente se experimentan al utilizar insertos con una profundidad de corte axial (ap) y fn mayores. Eso incluye riesgos de sobrecarga y, a ap y fn más bajos, riesgo de virutas largas. De este modo, las operaciones de mecanizado pueden ejecutarse a una fn mucho mayor para mejorar el control de la viruta, la estabilidad, la seguridad del proceso y la vida útil de la herramienta. Para los fabricantes, el cumplimiento de estos estándares más elevados de calidad y eficiencia puede lograrse aplicando mejoras en la fase de mecanizado.
Las ventajas del método PrimeTurning se refuerzan aún más con el software digital Tool Path, un generador de recorrido de la herramienta en línea específico, que suministra técnicas y códigos de programación de control numérico (NC) para configurar los parámetros y variables adecuados para una aplicación de mecanizado concreta. Cuando estos datos de corte precisos se utilizan en combinación con las herramientas de corte es posible conseguir ángulos de posición más pequeños, un uso eficiente del filo y sin atasco de viruta.
Aumento de la productividad
En un caso documentado de un cliente del sector automotriz de Sandvik Coromant, se buscaba lograr una operación de desbaste de una pieza de acero DIN 48CrMoV6-7 en un torno EMAG VSC 250. El cliente pretendía alcanzar mayores niveles de productividad y vida útil de las herramientas en su producción en serie, pero comprendió que los ajustes en los datos de las herramientas no serían suficientes. Por eso, aunque se tratara principalmente de una operación de desbaste, decidieron realizar un torneado exterior discontinuo y refrentado mediante el método PrimeTurning.
Se utilizaron entonces herramientas CoroTurn tipo B frente a los insertos existentes del cliente para evaluar las ventajas de rendimiento de la herramienta de conformación. Cada herramienta se utilizó con una velocidad de corte (vc) idéntica de 180 m/min y una profundidad de corte axial (ap) de 1.5~1.8 mm. Sin embargo, la CoroTurn® Prime tipo B de segunda generación funcionó a una fn más del doble de alta, 0.65 mm/rev, frente a los 0.3 mm/rev del inserto de la competencia.
Aunque la vida útil de cada plaquita era aproximadamente la misma, 9.58 min para el inserto de la competencia frente a 10 min para el inserto de las nuevas herramientas, se percibió una diferencia significativa en la productividad. La herramienta previa demostró una vida útil de tan solo 25 piezas con un tiempo de corte de 23 segundos por pieza. Sin embargo, la vida útil de la plaquita de las nuevas herramientas, de 50 piezas; es decir, duplicó con creces esta cifra, ya que solo se emplearon 12 segundos —aproximadamente la mitad del tiempo— en cada pieza. En adición se tuvo un desgaste del filo más predecible y un mejor control de la viruta.
Este tipo situaciones tan particulares, como el caso del maquinado de nuevos materiales, representan los retos que todos los días está enfrentando la manufactura de vehículos eléctricos. El desarrollo de nuevas tecnologías y su correcta evaluación e implementación serán la diferencia para que los fabricantes se mantengan competitivos en un mercado donde las barreras de entrada parecen estar cambiando radicalmente.
Otros artículos de interés
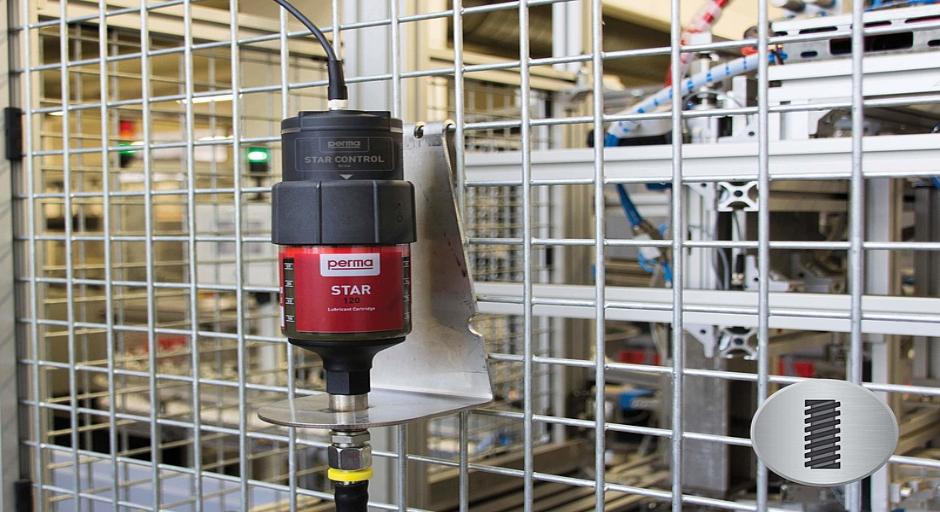
Lubricación automatizada, paso obligado en operación: Perma
En las plantas industriales, la lubricación ha pasado de ser una rutina
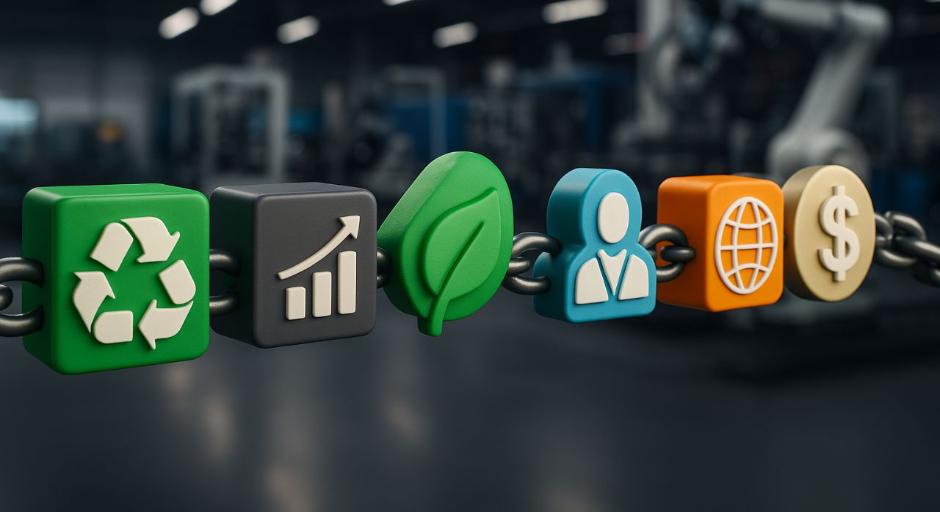
Cuidado ambiental: responsabilidad eslabonada
El cumplimiento de políticas de sostenibilidad en la industria manufacturera se ha
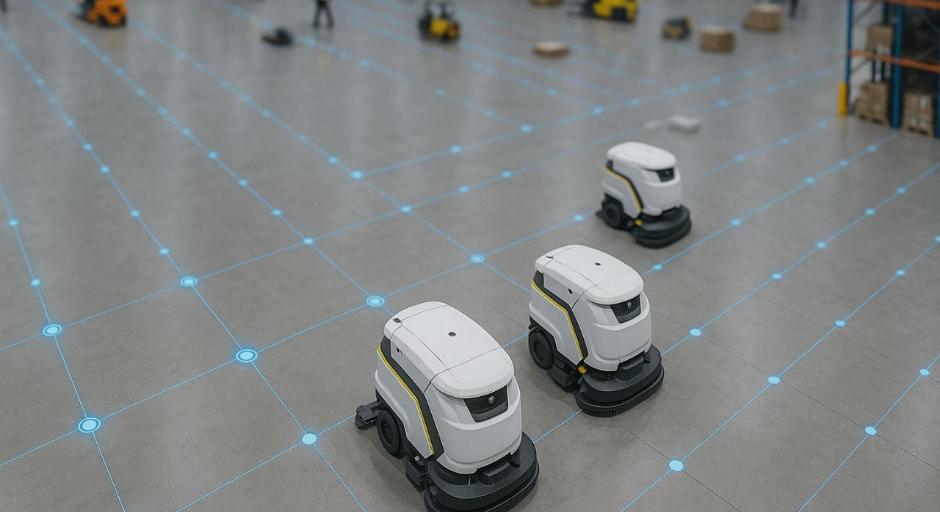
Limpieza industrial no escapa de la automatización
En la industria, la limpieza de áreas productivas es tan importante como

Suministro ininterrumpido para la Industria 4.0
La Industria 4.0 representa un salto evolutivo en la manufactura: sistemas físicos,
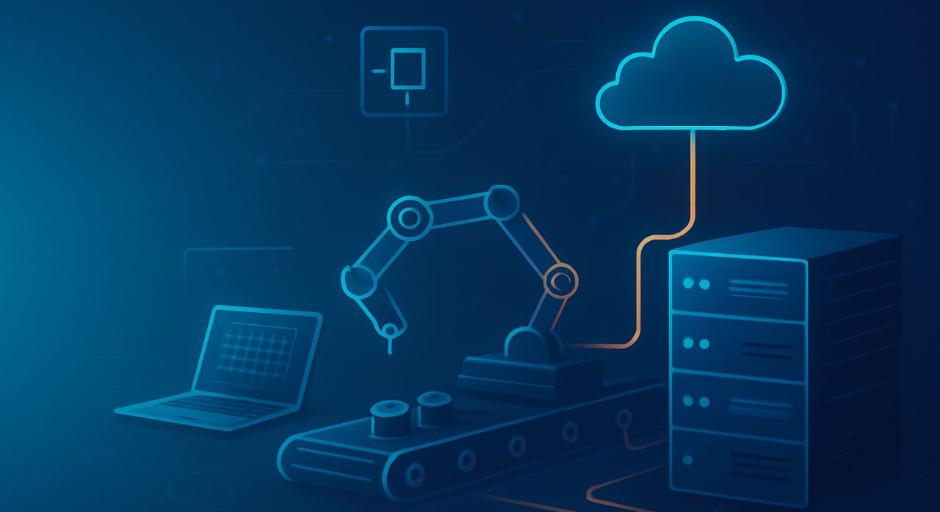
Por qué la manufactura requiere una buena infraestructura de redes
Con la adopción de tecnologías digitales en la manufactura, la infraestructura de

Transporte multimodal gana valor en la industria
En la industria manufacturera mexicana, la logística ha dejado de ser un